Total Product: Understanding Production Output in Economics
Key Takeaways
- Total product represents the total quantity of output produced by a firm with given inputs.
- Importance of total product includes understanding production capacity, efficiency, and resource allocation.
- Calculation of total product involves analyzing input-output relationships.
- Implications for businesses include insights into productivity, cost management, and strategic planning.
Introduction
Total product is a fundamental concept in economics that measures the total quantity of output produced by a firm using a given set of inputs. It provides a comprehensive view of a firm’s production capacity and efficiency. At ivyleagueassignmenthelp.com we help and guide students to delves into the concept of total product, its calculation, and its implications for optimizing production processes.
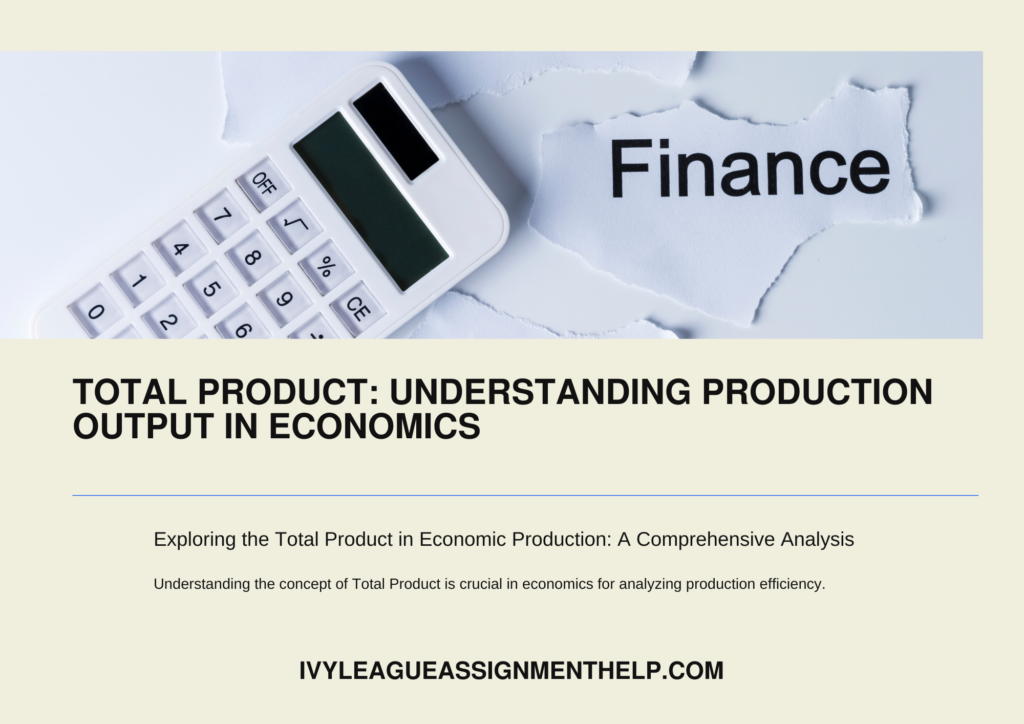
What is Total Product?
Definition of Total Product
Total product (TP) refers to the total quantity of goods or services produced by a firm during a specific period, given a certain amount of inputs such as labor, capital, and raw materials. It is a measure of a firm’s overall production output.
Importance of Total Product
Understanding total product is essential for several reasons:
- Production Capacity: It helps firms assess their production capacity and identify potential bottlenecks.
- Efficiency: Analyzing total product provides insights into how efficiently inputs are being converted into outputs.
- Resource Allocation: It aids in optimizing the allocation of resources to maximize production output and minimize costs.
Calculating Total Product
Input-Output Relationship
The calculation of total product involves understanding the relationship between inputs and outputs. By measuring the quantity of inputs used and the resulting output, firms can determine their total product.
Example Calculation
Suppose a factory employs 10 workers and produces 100 units of a product in a day. The total product in this case is 100 units. If the number of workers is increased to 15 and the output rises to 150 units, the new total product is 150 units.
Calculating Total Product
Number of Workers | Total Product (Units) |
---|---|
10 | 100 |
15 | 150 |
Factors Affecting Total Product
Labor
The quantity and quality of labor significantly impact total product. Skilled and motivated workers can produce more output, increasing the total product.
Capital
Capital, including machinery, equipment, and technology, plays a crucial role in determining total product. Advanced and efficient capital can enhance production capacity and output.
Technology
Technological advancements can improve production processes, leading to higher total product. Automation, improved machinery, and better production techniques contribute to increased output.
Raw Materials
The availability and quality of raw materials influence total product. High-quality inputs can result in higher-quality outputs and increased production efficiency.
Economies of Scale
Economies of scale occur when increasing the scale of production leads to a lower cost per unit of output. This can result in a higher total product as production becomes more efficient.
Total Product and Production Functions
Short-Run Production Function
In the short run, at least one factor of production is fixed. The short-run production function examines how varying the quantity of variable inputs, such as labor, affects total product while holding fixed inputs constant.
Law of Diminishing Returns
The law of diminishing returns states that as more units of a variable input are added to a fixed input, the additional output produced by each additional unit of the variable input eventually decreases. This principle affects the total product in the short run.
Example of Diminishing Returns
If a factory with a fixed number of machines hires additional workers, the initial increase in labor may lead to a significant increase in total product. However, after a certain point, adding more workers results in smaller increases in total product, as the fixed machines become a limiting factor.
Long-Run Production Function
In the long run, all factors of production are variable. The long-run production function analyzes how varying all inputs affects total product. Firms can adjust the quantities of labor, capital, and other inputs to achieve optimal production levels.
Implications of Total Product
Optimizing Resource Allocation
Understanding total product helps businesses optimize resource allocation to maximize output. By analyzing the input-output relationship, firms can make informed decisions about how to allocate labor, capital, and raw materials efficiently.
Improving Production Efficiency
Total product analysis provides insights into how to improve production efficiency. By identifying factors that contribute to higher output and lower costs, businesses can implement strategies to enhance productivity and streamline operations.
Strategic Planning
Total product is a valuable tool for strategic planning. It helps businesses forecast future production levels, assess the impact of technological advancements, and evaluate the potential benefits of scaling up production.
Real-World Case Studies
Case Study 1: Toyota’s Lean Manufacturing
Toyota’s implementation of lean manufacturing principles is a prime example of optimizing total product to achieve higher efficiency and productivity. Lean manufacturing focuses on eliminating waste, improving processes, and maximizing value. By adopting practices such as Just-In-Time (JIT) inventory management and continuous improvement (Kaizen), Toyota has been able to streamline its production processes, reduce costs, and increase output.
Impact on Total Product:
- Increased Efficiency: By minimizing waste and optimizing resource use, Toyota has increased its total product, resulting in higher output with fewer inputs.
- Cost Reduction: Lean practices have significantly reduced production costs, allowing Toyota to maintain competitive pricing and profitability.
- Quality Improvement: Continuous improvement and stringent quality control measures have enhanced the overall quality of Toyota’s products.
Case Study 2: McDonald’s Supply Chain Optimization
McDonald’s success in maintaining a consistent and efficient supply chain is another example of effective total product management. The fast-food giant has developed a highly efficient supply chain to ensure that its restaurants worldwide receive fresh ingredients and supplies promptly.
Impact on Total Product:
- Consistency and Quality: McDonald’s supply chain efficiency ensures that its products maintain consistent quality across all locations.
- Cost Efficiency: Optimized logistics and inventory management have reduced operational costs, contributing to higher profitability.
- Scalability: McDonald’s efficient supply chain allows the company to scale its operations quickly and efficiently to meet growing demand.
Factors Affecting Total Product
Factor | Description | Impact on Total Product |
---|---|---|
Labor | Quantity and quality of human effort | Skilled labor increases output |
Capital | Machinery, equipment, and technology | Advanced capital enhances production |
Technology | Technological advancements | Automation improves efficiency |
Raw Materials | Availability and quality of inputs | High-quality materials boost output |
Economies of Scale | Increased production efficiency | Lower costs lead to higher total product |
Frequently Asked Questions
What is total product?
Total product (TP) refers to the total quantity of goods or services produced by a firm during a specific period, given a certain amount of inputs such as labor, capital, and raw materials. It measures a firm’s overall production output.
Why is total product important?
Total product is important because it helps firms assess their production capacity, efficiency, and resource allocation. It provides insights into how efficiently inputs are converted into outputs and aids in optimizing production processes.
How is total product calculated?
Total product is calculated by measuring the quantity of inputs used and the resulting output. For example, if a factory employs 10 workers and produces 100 units of a product, the total product is 100 units.
What factors affect total product?
Factors affecting total product include labor, capital, technology, raw materials, and economies of scale. Skilled labor, advanced capital, technological advancements, high-quality raw materials, and increased production efficiency contribute to higher total product.
How does the law of diminishing returns relate to total product?
The law of diminishing returns states that as more units of a variable input are added to a fixed input, the additional output produced by each additional unit of the variable input eventually decreases. This principle affects the total product in the short run, as adding more variable inputs leads to diminishing marginal returns.
One thought on “Total Product: Understanding Production Output in Economics”