Cost Minimization: Strategies for Enhancing Business Efficiency
Key Takeaways
- Cost minimization involves strategies to achieve the lowest possible cost of production while maintaining output quality.
- Importance of cost minimization includes enhancing business efficiency, improving profitability, and gaining a competitive edge.
- Strategies for cost minimization include optimizing resource use, improving production processes, and leveraging technology.
- Implications for businesses involve better resource allocation, cost control, and strategic planning.
Introduction
Cost minimization is a critical concept in business economics that focuses on reducing production costs while maintaining output quality. Effective cost minimization strategies help businesses enhance efficiency, improve profitability, and gain a competitive edge in the market. At ivyleagueassignmenthelp.com we help and guide students to delve into the concept of cost minimization, its significance, and the strategies businesses can implement to achieve it.
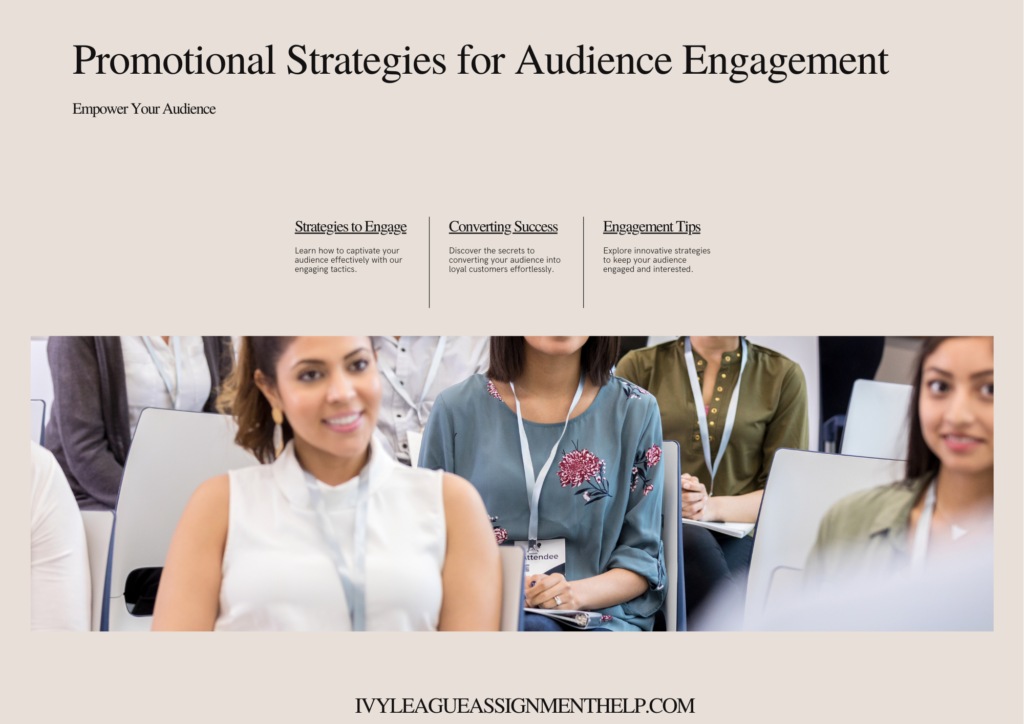
What is Cost Minimization?
Definition of Cost Minimization
Cost minimization refers to the process of achieving the lowest possible cost of production for a given level of output. This involves optimizing the use of resources, improving production processes, and implementing cost-saving measures.
Importance of Cost Minimization
Understanding and implementing cost minimization strategies are essential for several reasons:
- Enhanced Efficiency: It helps businesses produce goods and services more efficiently.
- Improved Profitability: Lower production costs lead to higher profit margins.
- Competitive Advantage: Cost-efficient firms can offer competitive prices and gain market share.
Strategies for Cost Minimization
Optimizing Resource Use
Efficient resource allocation is crucial for minimizing costs. Businesses need to ensure that labor, capital, and raw materials are used optimally to maximize output and minimize waste.
Improving Production Processes
Enhancing production processes involves adopting best practices, lean manufacturing principles, and continuous improvement strategies. Streamlined processes reduce inefficiencies and lower production costs.
Leveraging Technology
Investing in advanced technology can lead to significant cost savings. Automation, artificial intelligence, and data analytics improve production efficiency, reduce errors, and lower labor costs.
Bulk Purchasing
Buying raw materials and supplies in bulk can reduce costs through volume discounts. Businesses should negotiate with suppliers to secure favorable terms and lower the cost per unit.
Outsourcing
Outsourcing non-core activities to specialized firms can result in cost savings. By focusing on core competencies and outsourcing tasks such as logistics, customer service, or IT support, businesses can reduce operational costs.
Energy Efficiency
Implementing energy-efficient practices and technologies can lower utility costs. Businesses should conduct energy audits and invest in energy-saving equipment to reduce their energy consumption and costs.
Inventory Management
Effective inventory management ensures that businesses maintain optimal inventory levels, reducing storage costs and minimizing the risk of stockouts or excess inventory. Techniques such as just-in-time (JIT) inventory management can help achieve this balance.
Training and Development
Investing in employee training and development improves workforce productivity and reduces errors. Skilled employees contribute to more efficient production processes and lower costs.
Strategies for Cost Minimization
Strategy | Description | Impact on Costs |
---|---|---|
Optimizing Resource Use | Efficient allocation of labor, capital, and materials | Maximizes output, minimizes waste |
Improving Production Processes | Adopting best practices and lean manufacturing | Reduces inefficiencies, lowers production costs |
Leveraging Technology | Investing in automation and advanced technology | Improves efficiency, reduces labor costs |
Bulk Purchasing | Buying raw materials in bulk | Secures volume discounts, lowers cost per unit |
Outsourcing | Contracting non-core activities to specialized firms | Reduces operational costs |
Energy Efficiency | Implementing energy-saving practices and technologies | Lowers utility costs |
Inventory Management | Maintaining optimal inventory levels | Reduces storage costs, minimizes stockouts |
Training and Development | Investing in employee training | Improves productivity, reduces errors |
Implications of Cost Minimization for Businesses
Enhanced Efficiency
Implementing cost minimization strategies enhances production efficiency. Businesses can produce more with fewer resources, reducing waste and optimizing processes.
Improved Profitability
Lower production costs lead to higher profit margins. By minimizing costs, businesses can improve their financial performance and increase profitability.
Competitive Pricing
Cost-efficient firms can offer competitive prices without compromising on quality. Competitive pricing helps attract more customers, increase sales, and gain market share.
Better Resource Allocation
Cost minimization ensures that resources are used optimally. Efficient resource allocation improves overall business performance and reduces unnecessary expenses.
Strategic Planning
Cost minimization is crucial for strategic planning. Businesses need to consider cost-saving opportunities when planning for growth, expansion, and investment. Strategic cost management helps achieve long-term business goals.
Real-World Case Studies
Case Study 1: Toyota’s Lean Manufacturing
Toyota’s implementation of lean manufacturing principles is a prime example of cost minimization. Lean manufacturing focuses on eliminating waste, improving processes, and maximizing value. By adopting practices such as Just-In-Time (JIT) inventory management and continuous improvement (Kaizen), Toyota has been able to streamline its production processes, reduce costs, and increase output.
Impact on Costs and Efficiency:
- Reduced Waste: Lean manufacturing minimizes waste in production processes.
- Improved Efficiency: Continuous improvement strategies enhance productivity and lower costs.
- Lower Inventory Costs: JIT inventory management reduces storage costs and minimizes excess inventory.
Case Study 2: Amazon’s Supply Chain Optimization
Amazon’s success in maintaining a consistent and efficient supply chain is another example of effective cost minimization. The fast-food giant has developed a highly efficient supply chain to ensure that its restaurants worldwide receive fresh ingredients and supplies promptly.
Impact on Costs and Efficiency:
- Optimized Logistics: Advanced logistics systems reduce shipping costs and delivery times.
- Efficient Inventory Management: Real-time inventory tracking minimizes stockouts and excess inventory.
- Lower Operational Costs: Efficient supply chain operations reduce overall operational costs.
Real-World Case Studies
Case Study | Key Strategies Implemented | Impact on Costs |
---|---|---|
Toyota’s Lean Manufacturing | Lean manufacturing, JIT inventory management | Reduced waste, improved efficiency, lower inventory costs |
Amazon’s Supply Chain Optimization | Advanced logistics, real-time inventory tracking | Optimized logistics, efficient inventory management, lower operational costs |
Challenges in Cost Minimization
Maintaining Quality
One of the main challenges in cost minimization is maintaining product quality. Businesses must ensure that cost-saving measures do not compromise the quality of their products or services.
Balancing Cost and Innovation
Investing in new technologies and innovation is crucial for long-term success. However, businesses need to balance cost minimization with investments in innovation to stay competitive.
Employee Resistance
Implementing cost-saving measures can sometimes face resistance from employees. Effective communication and employee involvement are essential for the successful implementation of cost minimization strategies.
Short-Term Focus
Focusing solely on short-term cost savings can lead to long-term issues. Businesses need to consider the long-term implications of cost minimization strategies to ensure sustainable growth.
Challenges in Cost Minimization
Challenge | Description | Mitigation Strategies |
---|---|---|
Maintaining Quality | Ensuring cost-saving measures do not compromise quality | Implement quality control measures, continuous monitoring |
Balancing Cost and Innovation | Balancing cost minimization with investments in new technologies and innovation | Strategic planning, prioritize long-term growth |
Employee Resistance | Overcoming resistance from employees to cost-saving measures | Effective communication, involve employees in decision-making |
Short-Term Focus | Avoiding short-term focus that leads to long-term issues | Consider long-term implications, focus on sustainable growth |
Frequently Asked Questions
What is cost minimization?
Cost minimization refers to the process of achieving the lowest possible cost of production for a given level of output. This involves optimizing the use of resources, improving production processes, and implementing cost-saving measures.
Why is cost minimization important?
Cost minimization is important because it helps businesses enhance efficiency, improve profitability, and gain a competitive edge. By reducing production costs, firms can increase profit margins, offer competitive prices, and allocate resources more effectively.
What are some strategies for cost minimization?
Strategies for cost minimization include optimizing resource use, improving production processes, leveraging technology, bulk purchasing, outsourcing, implementing energy-efficient practices, effective inventory management, and investing in employee training and development.
What are the challenges in cost minimization?
Challenges in cost minimization include maintaining product quality, balancing cost and innovation, overcoming employee resistance, and avoiding a short-term focus that leads to long-term issues. Businesses need to implement strategies to mitigate these challenges effectively.
How does cost minimization impact business efficiency?
Cost minimization enhances business efficiency by optimizing production processes, reducing waste, and improving resource allocation. Efficient operations result in lower production costs, higher productivity, and better overall business performance.